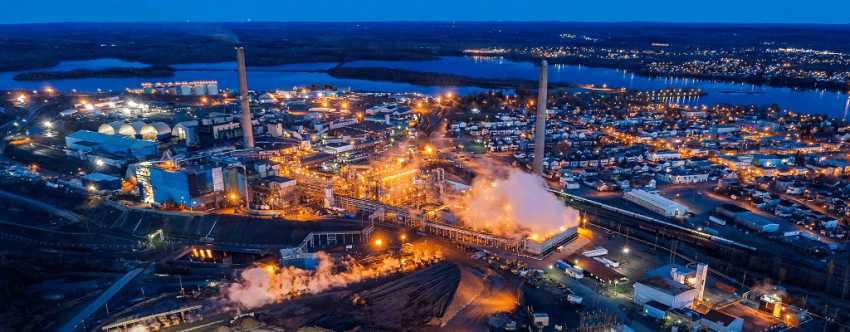
Where we've been - Traditional metals production
By default, we often think exclusively about the traditional flowsheet for metals production; the processing of primary mined materials in primary smelters. This usually incorporates some recycling of waste/scrap/residue material from downstream industries, often referred to as secondary raw materials. This is limited by the chemistry used to process the majority primary concentrate feed. The large-scale processing of secondary raw materials has typically been carried out in much smaller scale, close to market secondary operations, usually via a simple process flowsheet. These plants using totally secondary raw materials feed. Base metals smelters such as copper, zinc and lead use sulphide raw materials and so their process chemistry is driven by the emission of sulphur as sulphur dioxide, we therefore say that they operate in the sulphur space. On the contrary smelters processing alumina or iron ore have oxide raw materials which generate carbon dioxide as part of the process chemistry, and we therefore say they operate in the oxide space. Smelters operating in the sulphur space have typically previously not worried about CO2 emissions, being focused more on the minimization of SOx and NOx. Primary smelters are very energy intensive, most notably in their electrical power usage and use of hydrocar-bon fuels, which makes them significant in the decarbonisation debate. The smaller scale, simple flowsheet secondary smelters are less energy intensive, and so naturally have lower CO2 emissions. If we compare raw materials activity, primary mining is also far more energy intensive than urban mining, driven by the scale of the operations involved.
The future may be secondary - but we really need primary & secondary
As we move further into the age of decarbonisation with the focus on energy usage and CO2 emissions the obvious path would appear to be to produce more metal through the secondary route. In fact, if we look at the emission data that is currently available such a hypothesis would be supported. But the real provenance of a lot of this data is currently unclear. Smelters are not all the same, their energy usage and emissions not only driven by process flowsheet but also by location. The latter defining not only process emissions such as the level of grid CO2 emissions for power but those related to the transport of raw materials to the smelter.By looking further into the use and then subsequent reuse of metals the argument becomes even less clear. The end use of metals means that it could be tens of years before the metal enters the recycling system, and there is also no "timetable" as to when this will actually happen as there would be with a mine. Currently recycling rates, with the exception of lead, are also very low, at around 25-30%. Thus, the huge tonnages of metal needed for decarbonisation are likely to not be available within the relevant timeframe.
Lead
The recycling figures for lead cover up its symbiosis with zinc. Most lead is mined as a co-product with zinc, and lead concentrates also bring silver and gold units into the metals processing system. If the world moves to a secondary-only lead industry by boosting the relatively easy recycling of lead-acid batteries, what happens to lead concentrates and their gold and silver? A zinc miner operating a mine that produces lead concentrate as a co-product needs to have a market for it to ensure the long-term economics of the overall mining operation. Furthermore, a typical secondary lead smelter whose process flowsheet is dedicated to processing batteries cannot process concentrates. It has no unit operations able to deal with the sulphur content or any way to recover the levels of the other valuable metals, the silver and gold, seen in lead concentrates. Clearly this is where we need both primary and secondary lead smelters.
Copper and Aluminium
The tonnage of these metals required for decarbonization cannot come solely from the secondary sector. There is not enough feed material, never mind plant capacity. The secondary plants are ideal for processing high quality metallic aluminium and copper scrap; just like lead-acid batteries with a short recycle loop. The large capacity primary units again better situated to process concentrates and the more difficult secondaries; the argument of raw materials from recycling vs problematic waste streams. Clearly, we need both primary and secondary copper and aluminium smelters.
Zinc
Zinc is different to the other metals. Firstly, its usage in galvanising is sacrificial and so new zinc units must be added to the metals processing system. These have to come from primary sources to ensure sufficient material in the cycle. Secondly, zinc has two distinct secondary industries. The first takes metallic residues from galvanizing and processes them to make high grade zinc oxide and chemicals. The primary zinc industry is dominated by the electrolytic process. These smelters cannot treat a metallic feed through the usual flowsheet. Some metallic secondaries could be added in the casting area. But the purity of the secondary would be critical this far down the process flowsheet. There is little opportunity to carry out any complicated process operations, any impurities in the secondaries would have to be dealt with by careful blending, limiting the amount that could be used. It would also mean that the production of high-grade zinc oxide would all have to come from primary sources rather than being able to use recycle material saving both energy and emissions. The second wing of the zinc secondary industry is totally symbiotic to the primary sector. It processes dust from EAF steelmaking to produce a dust suitable for feeding into primary zinc smelters, thereby dealing with an extremely hazardous waste material, but add-ing a potentially large Scope 2 or 3 emission to the overall processing of zinc.
Nickel
Nickel consumption is dominated by Class 2 products which are ferro alloys used in stainless steelmaking, comprising around 69% of the nickel market. The remainder (Class 1 products) are nickel chemicals for the new battery technologies. Currently the recycling of nickel revolves around the reuse of various scraps in the manufacture of stainless steel. However, the recycling of nickel from "Black Mass", a multi-metal residue from used batteries, will soon become a critical strand in the move towards decarbonisation. But what will these plants look like? Many of the proposed processing routes have yet to get off the laboratory bench. Battery recycling is usually the province of secondary operations, but the tonnage involved, and potential metallurgical complexity lends itself to the primary sector.
E-Scrap
A web search reveals that electronic scrap (e-scrap) also referred to as electronic waste (e-waste) or WEEE (Waste Electrical and Electronic Equipment) is defined as :
"...all items of electrical and electronic equipment and its parts that have been discarded by its owner as waste without the intent of re-use"
Or more formally :
"...any electronic device with a circuit board or cathode ray tube (CRT) that no longer is needed and has exceeded its desired or usable life and would be destined for disposal. This includes but not limited to CPU's, laptops, monitors, televisions, copiers, cell phones, uninterruptable power supply (UPS) systems, and game consoles"
The content of e-scrap varies but typically there are significant amounts of copper, silver and gold that need to be recycled. However, growth in the recycling of e-scrap is slow, beset by various difficulties. There is concern about uncontrolled recycling operations in developing countries along with the large quantities that are simply landfilled. It has been reported that around 60% of the e-scrap produced is not recycled. In fact, in 2019, during the COVID pandemic, the UN reported that only 17.4% of the 53.6 million tonnes of e-scrap that was generated globally was collected and recycled.
A key issue appears to be, what is e-scrap? It is clearly a mixture of metals, some of which are vital to decarbonisation, plus a significant amount of plastic (according to BIR up to 30%). It is made up of a diverse range of material, meaning one type of e-scrap is likely metallurgically and physically different to another; for instance, a computer monitor versus a laptop computer. This highlights three key issues with urban mining in comparison to traditional primary mining.
Identification : in primary mining the geology of the ore body is known, and agreed assays are used for the concentrate to be smelted; for e-scrap?
Separation : in primary mining a mine plan is put into place the mineral processing circuit configured to ensure that the product assay is adhered to
Logistics : in primary mining the logistics from ore-body to saleable metal are clear and often well established
Once the metallic constituents of the e-scrap are known the metallurgical process to recover them is often pyro-metallurgy. Existing primary or secondary copper or lead processing circuits at smelters such as at Trail (Canada), Ronnskar (Sweden) and Hoboken (Belgium) are good examples.
The logistics for the collection, sampling and segregation of potentially small tonnages of variable e-scrap, when transboundary movement is often heavily constrained, is more challenging than that for primary concentrates.
In terms of emissions, it means we must also consider the top of the recycling triangle.
Thus, the upstream (pre-smelting) Scope 3 emissions (or potentially Scope 2 depending how these operations are defined) are significant factors for e-scrap, as well as the Scope 1 & 2 of the subsequent processing operations; alongside potentially difficult ESG questions about how the e-scrap is collected and sorted. An answer needs to be found to deal with the huge tonnage of e-scrap generated now and into the future, but both primary and secondary smelters will be the answer.
More questions than answers: Skarn's secondary research journey
Replacing primary production with secondary is not the simple solution to reducing GHG emissions it might appear. Urban mining cannot simply replace primary, although they are complementary.
Skarn will continue to develop our energy and emissions research to account for urban mining and secondary feed to primary smelters; especially for zinc and nickel. We will also look at secondary offerings to help explain more about this industry in terms of its true decarbonisation qualifications, notably for lead.
MORE FROM SKARN
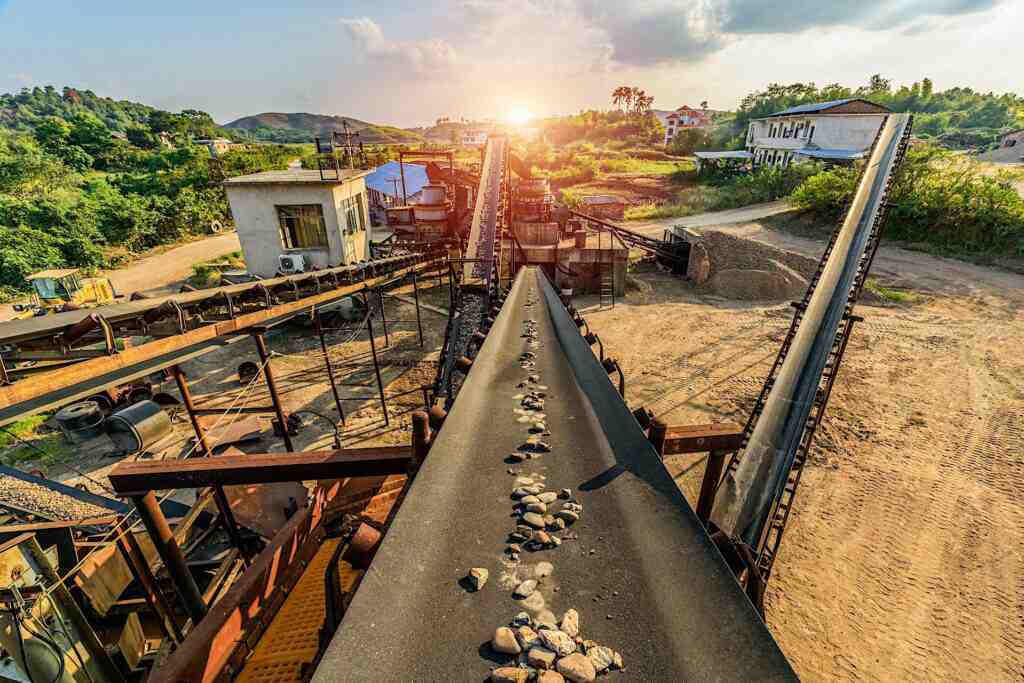
About Us
Skarn Associates is the market leader in quantifying and benchmarking asset-level greenhouse gas emissions, energy intensity, and water use across the mining sector.