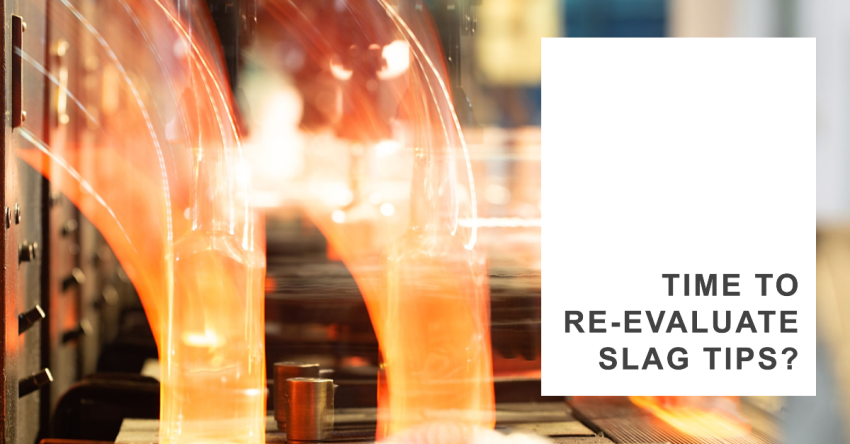
Urban mining beyond the main metals
So, what’s what with Slag Tips?
For every metallic mine and smelter, there is a considerable tonnage of waste material left behind in heaps, tips, dumps and dams. This is driven by many factors, including the head grade of the ore, the metal grade of the concentrate, the skill of the mining operations and the technical recovery of minerals processing and smelting operations.
Over the years it has become economic to reprocess some of these waste piles. Recovery of gold from South African tailings dams and that of high-quality coal from slag tips in South Wales to “sweeten” current production are two examples of large-scale ventures. But around the world many, many piles remain; often a legacy to the mine or smelter which has long closed.
The main concern for them is environmental, with the potential of pollution to groundwater and the air. However, it must be remembered there is still some value left in these tips. Modern smelting and mining techniques are typically far more efficient than when activity started on the site, so old residues may have quite high levels of value within them.
There is however a large ‘but’! These piles are often huge with potentially millions of tonnes of variable material making them up; a case of the good, the bad and the ugly!
As such a very detailed sampling exercise is required to understand what is in the specific pile and where value is situated geometrically. Further, this spatial spread of value, never mind the technology necessary, may render any recovery exercise uneconomic, as processing many thousands of tonnes to get a few hundred is always a difficult equation.
Most tip reprocessing and recovery operations typically focus on the main metal or metals recovered by the original operation. The slag tip at a base metal smelter is looked at usually only for copper, zinc and lead. In the feeds to these plants there were many more elements, most of which the smelter never recovered even during its operation. As we move further into decarbonisation, the need for more esoteric materials as part of batteries and electronics will also increase. These may be available through the processing of freshly mined materials, but what about their presence in urban mines where they typically have never been fully investigated?
Avonmouth – the Bristol Gold Mine?
For example, plan data for the Avonmouth ISP in Bristol, UK, has been analysed to see what elements were shown to be present in the slag from the ISF (Imperial Smelting Furnace). This material was water granulated and dumped into a large managed slag tip.
Model Feed & ISF Slag Compositions for Avonmouth
Following the closure of the ISP in 2003, this was simply capped and remains there today. The plan data was for one month of operation and this has been annualised to show the amount of each element in the feed and its subsequent deportment to the ISF slag. Under this plan the ISP would have produced around 109kt of zinc from around 122kt of zinc in feed.
Clearly the establishment of a recycling operation to recover the main metals produced from an ISF operation, zinc and lead, would be a complete waste of energy. However, looking at the list a number of the “new” critical metals could well be worth recovering, namely Nickel (Ni), Cobalt (Co), Chromium (Cr), Molybdenum (Mo), Germanium (Ge) and Gallium (Ga).
There is always a ‘but’….
Before we all rush to Bristol, there is another ‘but’! Even if we are happy that the dissemination of materials within the pile can be economically overcome, the valuable material recovered is going to be in a glass-like structure as ISF slag is water granulated to aid handling and storage, and likely with a number of the required materials mixed together.
The ability and economics of the extraction and separation of the various minerals, and ensuring that they are in the correct chemical form (oxide, carbonate, sulphate) for future use, is therefore another key factor in the overall reprocessing equation.
There are really only two options:
1. A pyrometallurgy route where the slag is remelted, and the various materials recovered to different phases or products. To ensure that the various materials can be recovered separately, final recovery from this product is likely to need some form of hydrometallurgical operation namely leaching and possibly solvent extraction.
2. A direct leaching of the slag to recover each material. To break down the slag matrix this is likely to need an aggressive media and several leaching steps will be necessary.
However, before the process route is finalised a significant laboratory and pilot testing program will be necessary to establish that it will work and to recover the materials required in their necessary chemical form. Clearly extracting specific materials from a slag tip is not easy or cheap, however it is a recycling operation and, when correctly managed, is green. Remember the primary production of battery and electronics raw materials is also not easy, cheap and in comparison, not that green!
As we move down the road of decarbonisation where less traditional materials are growing in importance, we need to look beyond the primary outputs of the original smelter and really understand what is in a pile. Is it now time to re-evaluate slag tips?
MORE FROM SKARN
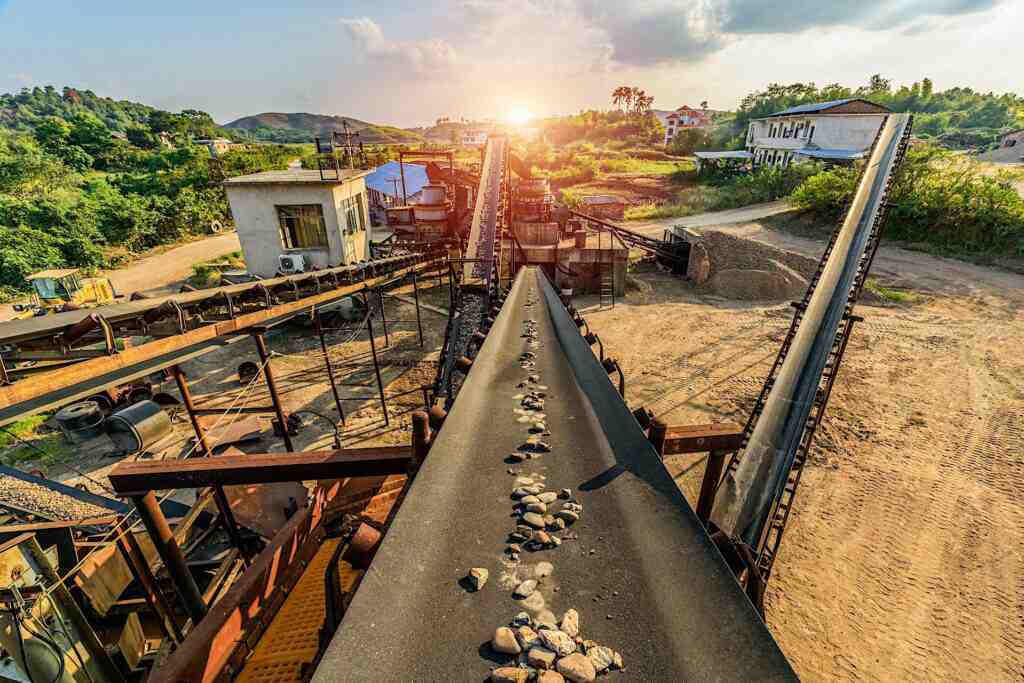
About Us
Skarn Associates is the market leader in quantifying and benchmarking asset-level greenhouse gas emissions, energy intensity, and water use across the mining sector.